CIPP – Cured In Place Pipe or Cured In Place Lining are rehabilitation techniques of underground and surface pipes. They consist in the insertion, into the existing pipe to be rehabilitated, of a resin-impregnated liner made of polyester felt or glass fibre woven or a combination of those materials. Before insertion, the liner is impregnated with polyester, vinylester or epoxy resin. Once inserted into the host pipe, it is inflated so that it may adhere well to the walls of the host pipe.
The resin-saturated liner is then cured through polymerisation of the resin with which it was impregnated. Polymerization occurs through the administration of heat (thermal curing) or radiating energy (UV light radiation). The result of this process is a new pipe, complete or not with structural functions, that conforms exactly to the host pipe, whatever its original shape.
Depending on the strength and thickness of the liner, a full structural functionality of the host pipe can be achieved.
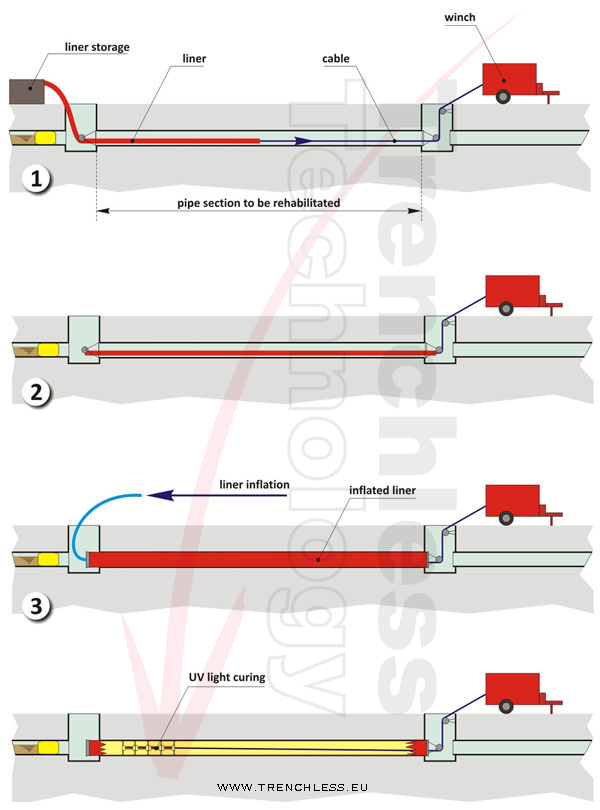
CIPP operational stages: insertion, inflating and curing of the liner.
DIMENSIONAL RANGES AND MATERIALS
-
any material.
-
LENGTH RANGES FROM 0,5 M (20 IN.) UP TO 400 M (1.300 FT) per shoot
-
DIAMETER RANGES FROM 25 MM (1 IN) TO 2.500 MM (98 IN)
If you are interested in CIPP you will find of interest the following case histories:
- PIPE BURSTING AND UV-CIPP AT THE FLORENCE AMERICAN CEMETERY OF THE WWII
- UV-CIPP OF A LARGE WATER PRESSURE PIPE
- DESIGN OF THE REHABILITATION OF LARGE DIAMETER SEWER MAINS BY CIPP
- UV-CIPP AT THE INTERNATIONAL AIRPORT OF ROME FIUMICINO
- CIPP TECHNOLOGY HANDBOOK
You can also find articles and papers related to CIPP in the following sections of the website: